Industrial IoT solutions connect factory equipment and data analytics to enable automated, data-driven workflows. Industrial IoT (IIoT) integrates sensors, machines, and cloud analytics to improve production visibility and control. These cutting-edge IoT solutions transform raw equipment data into real-time, actionable intelligence—empowering operators to pinpoint inefficiencies, streamline operations, and drive peak performance on the fly. Over time, the adoption of smart manufacturing platforms has accelerated: for example, analysts project that IoT-driven optimization could add over US$14 trillion to the global economy by 2030. In practice, modern factories use IoT solutions to automate manual operations and achieve unprecedented levels of efficiency and quality.
IoT Solutions Architecture and Key Components
A typical Industrial IoT solution follows a multi-layer architecture that links sensors, controllers, and analytics platforms. Factory sensors (e.g., vibration, temperature, pressure, or image) collect high-frequency data from equipment and products. This raw data is first handled by local edge devices or gateways, which perform preliminary processing and enforce security. Then the cleaned data is sent over reliable networks (wired or wireless) to a cloud or on-premises IoT platform for deep analysis. The figure below shows a simplified data flow in an IIoT architecture:
mermaid
flowchart LR
Sensor([Sensors on Equipment]) –> Edge([Edge Gateway])
Edge –> Cloud([Cloud Platform])
Cloud –> Analytics([Analytics & AI])
Analytics –> Dashboard([Operations Dashboard])
Analytics –> Controller([Actuation/Control])
Key components of an IoT solution include:
- Sensors and Actuators: Industrial sensors are embedded in machines to measure parameters like temperature, vibration, speed, and pressure. These IoT solutions use sensor data to detect faults or quality issues (e.g., detecting an out-of-spec vibration signal). Actuators (like motors or valves) can automatically respond to control signals, closing the loop from data to action.
- Edge Devices/Gateways: Edge computing devices aggregate data from multiple sensors locally. They filter and preprocess data to reduce bandwidth needs and issue real-time control commands. For instance, an edge gateway might close a valve if a critical threshold is reached before sending data upstream. This reduces latency and ensures critical commands are executed even if connectivity is intermittent.
- IoT Connectivity and Protocols: Reliable, industrial-grade connectivity (Ethernet, Wi‑Fi, 5G, LoRaWAN, etc.) links equipment to the network. Standard protocols (MQTT, OPC UA) ensure disparate machines can communicate with the IoT platform. Robust networking is a cornerstone of IoT solutions in manufacturing, enabling seamless data flow between machines and servers.
- Cloud Platform and Analytics: The cloud or central server hosts IoT software that ingests and stores all production data. Machine learning and AI modules analyze the data at scale to spot patterns and anomalies. For example, advanced analytics can model equipment health to predict failures or optimize production schedules. Process historians and databases provide a unified view of all assets.
- User Interfaces and Dashboards: Operators and managers use web or mobile dashboards to visualize key metrics and system alerts. Well-designed dashboards (often part of an IoT platform) show machine uptime, productivity, and quality KPIs in real time, so decision-makers can act quickly.
By combining these components, IoT solutions form a connected, automated manufacturing ecosystem. Industrial routers or PLCs bridge shop-floor hardware with IT systems, and data lakes store historical information for long-term optimization. In sum, the layered architecture of sensors → edge → cloud → analytics enables factories to extract value from every data point.
Benefits of IoT Solutions in Manufacturing Efficiency
IoT solutions deliver measurable gains in efficiency, quality, and sustainability on the plant floor. Through intelligent automation of data collection and instant, actionable insights, they slash downtime and eliminate costly human errors. Manufacturing leaders report that connected systems allow robotic equipment to coordinate autonomously and perform self-optimizations, greatly improving throughput. In practice, IoT solutions can boost overall equipment effectiveness (OEE) by exposing bottlenecks and triggering timely maintenance actions. Key benefits include:
- Predictive Maintenance: Sensors continuously monitor machine health (vibration, heat, pressure). Advanced analytics detect early warning signs of wear or misalignment, allowing maintenance teams to intervene before failure. Research reveals that IoT-powered predictive maintenance can slash equipment failures by nearly 70% while trimming maintenance expenses by roughly a quarter, transforming reactive fixes into proactive, cost-saving strategies. This drives higher uptime and productivity.
- Improved Efficiency and Throughput: Automated workflows enabled by IoT increase production speeds. For example, connected machines share status data to self-sequence tasks (assembly, material handling, etc.) without human coordination. According to cutting-edge industry research, the full-scale integration of IoT across manufacturing could unlock staggering annual productivity gains, somewhere between 1.2 trillion and 3.7 trillion, as early as 2025. Real-time feedback loops let engineers rapidly fine-tune processes based on actual performance data.
- Energy Optimization: IoT energy meters and power sensors track the electricity usage of equipment in real time. Detailed energy dashboards identify inefficiencies, enabling targeted improvements (e.g., shutting down idle machines or optimizing setpoints). In a documented instance, the implementation of a real-time IoT-based monitoring system on an industrial production line enabled a manufacturing entity to achieve a ~40% reduction in energy expenditure through optimized operational efficiency. This reduces operational utility costs and advances organizational sustainability objectives.
- Quality Control and Yield: High-resolution IoT sensors detect product quality issues early. For instance, smart cameras and force sensors can flag defects or material variances, prompting corrective actions on the fly. Automating inspection reduces scrap and rework. Data analysis also uncovers root causes of quality lapses (e.g., a specific machine drift), enabling process refinement. As one report notes, digitization and IoT-enabled automation have achieved over 65% reduction in product deviations in advanced factories.
- Supply Chain and Asset Management: Real-time tracking of work-in-progress, inventory, and logistics avoids delays and stockouts. IoT-enabled asset tracking systems leverage RFID tags and GPS-embedded devices to provide real-time monitoring and traceability of material movement across supply chains. According to industry surveys, 78% of supply chain leaders are deploying IoT technologies to increase speed and automate manual tasks. Better visibility reduces buffer inventory and ensures parts arrive just-in-time, smoothing production flow.
By harnessing these benefits, manufacturers can operate leaner, respond faster to demand changes, and reduce operational costs. The data-driven insights from IoT solutions not only improve current operations but also feed continuous improvement cycles across the plant.
Best Practices for Implementing IoT Solutions
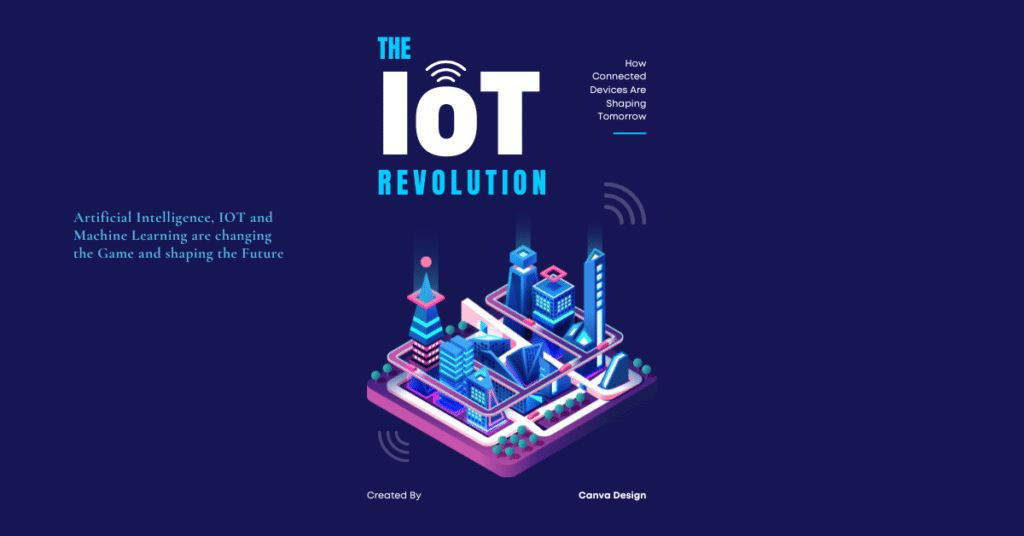
Successful deployment of Industrial IoT solutions requires careful planning and cross-functional coordination. Manufacturers should follow these best practices to maximize ROI and minimize risk:
- Pilot Projects with Clear KPIs: Start with targeted pilot deployments on critical machines or production lines. Define specific goals (e.g., reduce unplanned downtime by X%, improve output by Y%). This methodology enables quantifiable performance evaluation and iterative learning, ensuring validated outcomes before operational expansion.
- Layered, Scalable Architecture: Use an open, modular architecture. Deploy industrial-grade sensors and edge gateways from known vendors. Choose robust networking (LTE/5G, Ethernet, or IoT radios) and protocols (MQTT, OPC UA) that scale. Guarantee seamless interoperability between newly deployed systems and incumbent Programmable Logic Controllers (PLCs), Manufacturing Execution Systems (MES), or Enterprise Resource Planning (ERP) platforms to maintain operational continuity and data integrity. Standardized IoT platforms simplify integration across diverse equipment.
- Edge-to-Cloud Strategy: Balance processing between edge and cloud. Perform time-critical monitoring and immediate alerts at the edge (low latency), while offloading heavy analytics and ML to the cloud. This hybrid approach reduces bandwidth use and keeps factory control resilient, even during network outages.
- Robust Security Framework: Protect IoT networks by design. Use encryption for data-in-transit, device authentication, and secure boot for controllers. Segment IoT traffic from corporate networks. Implement continuous monitoring and anomaly detection (often using AI) to spot cyber intrusions. This is critical because industrial IoT environments face threats from hackers and insider errors.
- Cross-Functional Team Collaboration: Involve both operations (OT) and IT engineering teams early. Operators understand production needs; IT/security teams handle network and data issues. Joint teams ensure that IoT solutions meet both functional requirements and technical standards. Continuous training and change management help plant staff adopt the new technology.
- Iterative Improvement and KPIs: After deployment, continuously measure performance against KPIs (OEE, downtime, yield, energy per unit). Use IoT dashboards to spot trends. Refine sensor placements, analytics models, and maintenance schedules based on real results. Over time, this iterative process drives further efficiency gains.
Following these steps helps ensure IoT initiatives deliver value. According to industry intelligence, major implementation challenges include cybersecurity, ROI justification, and integration complexity. Addressing these proactively—as above—helps industrial organizations overcome barriers and fully leverage IoT solutions.
Conclusion
Industrial IoT solutions are reshaping manufacturing by enabling highly efficient, agile production. Connected sensors and analytics empower factories to predict problems, automate tasks, and continuously improve processes. As a result, manufacturers gain higher throughput, lower waste, and safer operations. Furthermore, IoT data unlocks new business models: for example, equipment makers now offer “machine-as-a-service” contracts—selling operating hours instead of machines—and use IoT feedback to guarantee uptime. In sum, well-implemented IoT solutions yield a strong ROI through cost savings and innovation, helping manufacturers stay competitive in the era of smart industry.
Mermaid Diagram: The IoT architecture diagram above illustrates how sensors, gateways, and cloud analytics interconnect in a smart manufacturing setup.
No responses yet